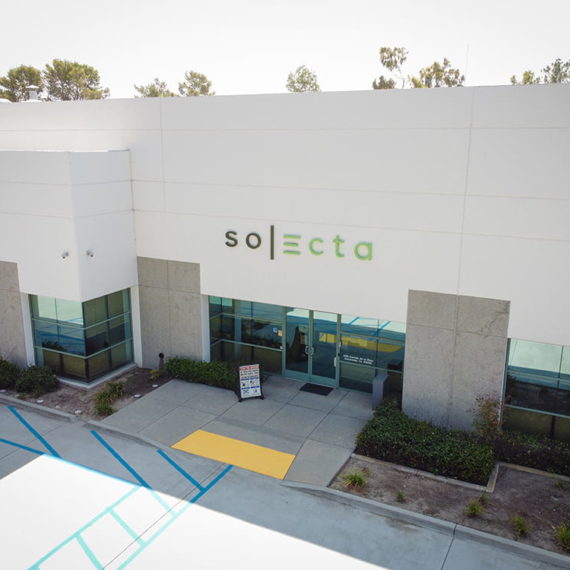
Careers
Join Us As We Revolutionize Separation Technologies.The Spirit Behind Solecta
Do you want to help make a big impact in the world?
Then you’re a great fit!
Our team is committed to playing an impactful role in the development of novel and critical separation technologies that directly support the improvement of the lives of an expanding world population.
Making Your Mark
Every one of our career opportunities plays a critical role in the success of our company. We’re looking for exceptional individuals with brains, grit and heart – who want to achieve great things.
Let’s do great things together.
Our Values
Client Success
Win as a Team
Dare to Shape the Future
Strive for Excellence
We Value Each Other
We Are Always Learning and Growing
Open Positions – Apply Below
Position Summary
As a member of Solecta’s commercial team, the Client Development Executive is responsible for the execution of the sales plan in accordance to company vision and strategy. In this position, the Client Development Executive will work with leaders and influencers across a variety of companies within the dairy, food ingredients, life sciences, and manufacturing market segments to help them solve unique and real issues. This role will report to the Vice President of Client Development and work collaboratively with the Market Segment Managers, Product Managers, Applications Engineering and Operations leadership to ensure financial goals are met while upholding our company values and culture of teamwork.
Essential Functions
- Finds and develops new opportunities at targeted prospects
- Identifies and nurtures valuable and relevant leads.
- Cultivates existing client relationships and evolve them into further business opportunities and client partnerships that ensure a healthy pipeline
- Accelerates complex sales cycles from prospect to close and beyond
- Identifies client needs and success criteria to advance the sales process. Develops value propositions leveraging products and services core to Solecta
- Creates long-term trust and client partnerships at multiple decision-making levels through a genuine consultative and problem-solving approach
- Investigates and discovers client purchasing and usage data to inform sales planning and market strategy development
- Develops and executes sales targets at all stages and orchestrate compelling interactions with prospective and existing clients
- Plans activity in accordance with commercial milestones
- Establishes aggressive yet realistic plans to achieve the desired sales plan objectives, anticipate risks, and have contingency plans to manage them
- Utilizes CRM to manage a sales portfolio, pipeline metrics, analytics, share information with commercial team, monitor sales cycles and stages, maintain pipeline to meet metrics
- Participates in the development of the sales annual operating budget and maintains expenses within the plan
- Partners with marketing and sales team to execute strategy, demand generation, lead development and communication to drive sales efforts
- Engages customers and creates personal brand using social media in accordance with Solecta guidelines
- Remains current on industry, market trends, developments, and technology trends within the membrane and element industry, while continuously learning about Solecta, its vision, culture and people
- Consistently improves knowledge of all products and services provided by competitors
- Learn all aspects of customer operations. Continuous development of technical and commercial skills
Position Qualifications
- Bachelor’s degree in Science, Business Administration or other related field; MBA preferred
- 5 years of sales, and business development experience with complex global manufacturing clients
- 5+ years of experience in company providing technical products and/or services, preferred
- Process membrane separations experience, preferred
- Proven track record of interpersonal skills with ability to cross-functionally interface with and positively influence other departments
- Strong leadership skills, independent thinking, proven organizational and planning abilities, and excellent analytical and problem-solving skills
- Ability to develop strategic relationships; strong verbal and written communication skills; excellent presentation skills
- Thrives in a fast-moving environment
- 50-75% travel required
- Remote worker position located near a major metropolitan area
The salary range for this position is $115,500 to $214,500. The actual salary offer will carefully consider a wide range of factors, including your skills, qualifications, job-related knowledge, experience and location.
EOE
Position Summary
The Director of Client Development serves as a member of the Solecta leadership team responsible for the execution of the sales plan in accordance to the company vision and strategy. In this position, the Director of Client Development will work with leaders and influencers across a variety of companies within company defined market segments helping them solve unique and real issues. This role will report to the CCO and work collaboratively with Product Management, Applications Engineering and Operations leadership to ensure financial goals are met while being uncompromising to company values and culture of teamwork and positivity.
Essential Functions
- Develop and execute sales targets at all stages and orchestrate compelling interactions with prospective and existing clients
- Develop new relationships by identifying and nurturing valuable and relevant leads
- Cultivate existing client relationships and evolve them into business opportunities and client partnerships that ensure a healthy pipeline for the company
- Create long-term client partnerships by understanding clients’ needs and business realities, whether clearly expressed or not, identified through a genuine consultative and problem-solving approach
- Partner with marketing to execute strategy, demand generation, lead development and communication to drive sales efforts
- Manage a sales portfolio, pipeline metrics, analytics, and company CRM, Salesforces.com
- Remain current on industry and market trends and developments, while continuously learning about Solecta, its vision, culture and people
- Contribute to and review product management analysis of new product channels or market segments that represent meaningful potential opportunity for the company
- Identify critical stakeholders and competitors within these channels/segments and characterize their strategic focus
- Recommend the best way to participate in these channels/segments – consistent with overall company vision, priorities, capabilities, and assets
- Determine customer needs and characterize the value proposition needed to win in the highest-priority channels/segments
- Determine how best to support these channels/segments and deliver the winning value proposition
- Interview, hire, coach, motivate, develop, recognize and manage performance of direct reports. Provide regular feedback to all direct reports. Set performance objectives, support development plans and monitor progress
- Establish aggressive yet realistic plans to achieve the desired sales plan objectives, anticipate risks, and have contingency plans to manage them
- Participate in the development of the sales annual operating budget and maintains expenses within the plan
- Other duties as assigned
Position Qualifications
- Bachelor’s degree in science, business administration or other related field; MBA preferred
- 10 years of strategic marketing, business development and/or consulting experience required
- 8+ years of experience in company providing technical products and/or services is preferred
- Clear, strategic thinking– proven ability to disaggregate complex issues, to develop a framework for understanding the critical elements of the problem, and to generate and stand behind recommendations that result from this analysis
- Leadership Presence– the ability to communicate effectively with senior members of the leadership team and board of directors
- Experience developing an annual financial plan and budget for a sales organization and maintaining compliance to the plan
- Proven track record of interpersonal skills with ability to cross-functionally interface with and positively influence other departments
- Strong leadership skills, independent thinking, proven organizational and planning abilities, and excellent analytical and problem-solving skills
- Advanced experience and competence in the use of CRM systems
- Firm, fair, and consistent approach to company policy and employee management
- Ability to “get the job done” and take responsibility for results with and without direct authority
- Ability to develop strategic relationships; strong verbal and written communication skills; excellent presentation skills
- Thrives in a fast-moving environment
The salary range for this position is $123,200 to $228,800. The actual salary offer will carefully consider a wide range of factors, including your skills, qualifications, job-related knowledge, experience and location.
EOE
Position Summary
The Senior Process and Equipment Engineer is responsible for improving existing and developing new membrane and element manufacturing and test equipment and processes. The successful candidate will use lean thinking, and statistical and robust engineering methodologies to develop new and improve existing equipment and improve existing processes that improve factory capabilities, reduce scrap and setup and improve plant throughput.
Essential Functions
- High energy with a strong work ethic; willingness to roll up one’s sleeves and learn.
- “Hands-on”; comfortable on the shop floor working with all levels of technical, professional, and managerial staff, operators and technicians.
- Good teamwork, time management, problem solving, and critical thinking skills. Customer orientation mindset.
- Investigate and resolve problems in production including troubleshooting equipment and process problems:
- Regularly monitor equipment and process performance to ensure operations meet safety, quality, and capacity/cycle time requirements.
- Solve problems using structured problem-solving methods. (ex: Ishikawa/fishbone, Six Sigma, A3, PDCA, root cause analysis, etc.)
- Perform data mining and data analysis.
- Perform root cause analysis of element and membrane product defects and implement short term containment/workarounds and long-term solutions.
- Assist maintenance personnel as required with troubleshooting and repair of equipment including reading and interpreting electrical schematics and manufacturers’ documentation related to plant equipment and plant facilities equipment maintenance.
- Design, build, and qualify new production and test equipment and processes:
- Analyze existing capacity and make recommendations of process and equipment improvements to maximize capacity, productivity and throughput.
- Define and conduct engineering tests for experimental data collection.
- Define, select, and develop new or modified processing concepts.
- Develop and execute new equipment build, existing equipment modification, and test and acceptance plans.
- Oversee and drive associated projects into manufacturing through the change control board, documentation and training.
- Communicate (written and oral) technical concepts clearly and concisely to audiences with varied levels of educational and technical backgrounds. Excellent influencing skills. Develop clear written instructions (including but not limited to: operations procedures, SWI’s/Standard Work Instructions, corrective and preventive maintenance and troubleshooting procedures, and RFC’s/Response Flow Checklists) and train staff.
- Lead Continuous Improvement efforts.
- Compile and evaluate test data to determine appropriate limits and variables (CTQs) for process or material specifications. Perform materials characterization.
- Evaluate product performance and opportunities for improvement.
- Collaborate with R&D and Operations to take product and equipment improvements from concept to production.
- Engage with and assist other professional staff including Finance, Sales, Marketing, Operations, Engineering, R&D, Supply Chain, and Quality.
- Comfortable working in a fast paced rapidly changing environment.
- Other duties as assigned.
Position Qualifications
Education and Experience:
- B.S. (M.S. preferred) in an Engineering discipline plus 8+ years of engineering experience in a manufacturing environment.
- Record of defining and managing manufacturing equipment and process improvement projects to completion. Ability to influence and facilitate process and behavior change.
- Proficiency with mechanical design packages (Solidworks, AutoCAD, etc.)
- Parts and equipment fabrication experience (machining, fabrication, electrical and mechanical assembly, welding, electrical box build)
- Strong project management skills
- Proficiency with MS Office, including Word, Excel and PowerPoint
Additional desired experience or willingness to learn:
- Working knowledge, and hands-on experience with industrial electricity and control systems including Allen Bradley PLC’s and controls integration, programming, and troubleshooting
- Working knowledge and hands-on experience with robotics such as Fanuc.
- Electrical troubleshooting skills including demonstrated ability to read and interpret P&ID’s and electrical schematics and diagrams, AC and DC circuit knowledge, ability to perform electrical tests, read results and diagnose and repair electrical problems.
- Understanding of general and preventive maintenance processes and methods.
- Demonstrated data analysis skills. Experience with DOE methodologies and with statistical packages such as JMP, Minitab, SPC, Matlab, etc.
- Experience in Lean, Six Sigma, Theory of Constraints and Taguchi methods.
- Exposure to statistical process control, DOE, robust engineering methodologies and engineering analysis tools.
- Exposure to Quality systems.
The salary range for this position is $67,200 to $124,800. The actual salary offer will carefully consider a wide range of factors, including your skills, qualifications, job-related knowledge, experience, and location. No relocation available.
EOE
This is a unique opportunity to work with world-class teammates and make a meaningful impact on the success of Solecta and the clients that we serve. It’s a great place to work – the enthusiasm is contagious and I’ve had more opportunity than ever to develop and enhance new skills. The future is bright at Solecta.
– Kevin, Client Development Executive
Join Our Team
We are always looking for talented, driven individuals to join our team.